Introduction to Solar Panel Types
Solar panels, the cornerstone of photovoltaic (PV) energy systems, come in two primary types: monocrystalline and polycrystalline. Understanding the differences between these two technologies is crucial for making an informed decision when investing in solar power. This section will explore the fundamental differences in their manufacturing, efficiency, and aesthetic qualities.
The fundamental difference between monocrystalline and polycrystalline solar cells lies in the structure of their silicon. Monocrystalline silicon is a single, continuous crystal lattice, while polycrystalline silicon is composed of multiple, smaller crystals fused together. This seemingly small difference significantly impacts the efficiency and cost of the resulting solar panels.
A Brief History of Monocrystalline and Polycrystalline Solar Cell Development
The development of both monocrystalline and polycrystalline silicon solar cells has been a parallel journey, marked by continuous improvements in efficiency and manufacturing processes. Early silicon solar cells, developed in the late 1950s, were primarily monocrystalline due to the superior purity and crystalline structure achievable through the Czochralski process (CZ). This method, however, is energy-intensive and expensive. The development of polycrystalline silicon casting methods in the 1970s offered a more cost-effective alternative, albeit with slightly lower efficiency. Since then, both technologies have seen significant advancements, with continuous improvements in efficiency and reductions in manufacturing costs driving the growth of the solar industry. Improvements in both technologies continue to this day, driven by research into material science and manufacturing techniques.
Manufacturing Process Comparison
The manufacturing processes for monocrystalline and polycrystalline solar panels differ significantly, impacting their final characteristics and cost.
Feature | Monocrystalline | Polycrystalline |
---|---|---|
Silicon Ingot Production | Czochralski (CZ) method: A seed crystal is rotated and slowly pulled from a molten silicon bath, creating a large, single crystal ingot. | Directional Solidification: Molten silicon is poured into a mold and allowed to cool and solidify, resulting in multiple crystals. |
Ingot Slicing | The single-crystal ingot is sliced into thin wafers using diamond-wire saws. | The polycrystalline ingot is sliced into wafers, often resulting in some material waste due to the irregular crystal structure. |
Cell Production | Wafers are processed to create solar cells, resulting in a uniform, dark-colored appearance. | Wafers are processed to create solar cells, resulting in a mottled, multi-colored appearance. |
Panel Assembly | Cells are assembled into panels using standard lamination techniques. | Cells are assembled into panels using standard lamination techniques. |
Efficiency and Energy Production
Monocrystalline and polycrystalline solar panels differ significantly in their energy conversion efficiency and long-term performance. Understanding these differences is crucial for making an informed decision when choosing a solar panel system for your needs. This section will delve into the efficiency and energy production aspects of both panel types, considering various factors that influence their performance over time.
The primary difference lies in the crystalline structure of the silicon used in manufacturing. Monocrystalline panels utilize a single, continuous silicon crystal, resulting in a more uniform and efficient structure. Polycrystalline panels, on the other hand, are made from multiple silicon crystals, leading to a slightly less efficient energy conversion process. This difference translates directly into the amount of electricity generated.
Efficiency Comparison Under Varying Conditions
Monocrystalline solar panels generally boast higher efficiency rates compared to polycrystalline panels. Under ideal conditions (high solar irradiance and optimal temperature), a monocrystalline panel can achieve an efficiency of around 20% or even higher, while a polycrystalline panel might reach 15-18%. However, this difference can be less pronounced under less-than-ideal conditions. For instance, in low-light situations, such as cloudy days or during early mornings and evenings, the efficiency gap might narrow somewhat, although monocrystalline panels generally retain a slight edge. Similarly, high temperatures can negatively impact the performance of both types, but monocrystalline panels often exhibit slightly better temperature coefficient characteristics, meaning their efficiency decreases less dramatically with increasing temperature.
Long-Term Performance and Degradation Rates
The long-term performance of solar panels is a critical factor to consider. Both monocrystalline and polycrystalline panels degrade over time, primarily due to factors such as ultraviolet (UV) radiation, temperature fluctuations, and potential induced degradation (PID). However, studies suggest that the degradation rates might differ slightly between the two types. While both typically experience a gradual decline in power output over their lifespan (usually around 25-30 years), monocrystalline panels are often cited as having slightly slower degradation rates, potentially maintaining a higher percentage of their initial power output after several years compared to polycrystalline panels. This difference is usually marginal and depends significantly on the quality of the manufacturing process and the environmental conditions.
Typical Power Output Curves Over Lifespan
The following hypothetical chart illustrates the typical power output curves for both monocrystalline and polycrystalline panels over a 25-year lifespan. Note that these are illustrative examples, and actual performance can vary depending on numerous factors.
Year | Monocrystalline Panel (kW) | Polycrystalline Panel (kW) |
---|---|---|
0 | 3.0 | 3.0 |
5 | 2.95 | 2.90 |
10 | 2.90 | 2.80 |
15 | 2.85 | 2.70 |
20 | 2.80 | 2.60 |
25 | 2.75 | 2.50 |
This table shows a hypothetical scenario where both a 3kW monocrystalline and a 3kW polycrystalline panel are installed. The monocrystalline panel maintains a higher power output throughout its lifespan compared to the polycrystalline panel. It’s important to note that these are simplified examples, and real-world performance will vary based on factors like panel quality, installation, weather conditions, and shading.
Cost and Return on Investment
Choosing between monocrystalline and polycrystalline solar panels often comes down to balancing upfront costs with long-term energy savings and system lifespan. While monocrystalline panels generally boast higher efficiency, leading to potentially faster ROI, polycrystalline panels offer a more budget-friendly initial investment. Understanding these cost differences and their impact on your return on investment is crucial for making an informed decision.
Polycrystalline panels typically have a lower upfront cost per watt than monocrystalline panels. This is because the manufacturing process for polycrystalline silicon is less energy-intensive and uses less refined silicon. This lower manufacturing cost translates directly to a lower price for the consumer. However, this lower initial cost needs to be weighed against the slightly lower energy production over the lifespan of the system.
Upfront Costs and System Pricing
The price difference between monocrystalline and polycrystalline solar panel systems of equivalent power output can vary depending on several factors, including location, installer, and system size. Generally, a polycrystalline system will be cheaper to purchase and install initially. For example, a 5kW system using polycrystalline panels might cost between $10,000 and $15,000, while a comparable system using monocrystalline panels might cost between $12,000 and $18,000. These are broad estimates, and it’s essential to obtain quotes from multiple installers in your area to get accurate pricing.
Long-Term Cost Savings and System Maintenance
While the initial cost is lower for polycrystalline systems, the long-term cost savings might favor monocrystalline panels due to their higher efficiency. Higher efficiency translates to more energy generated over the system’s lifetime, potentially offsetting the higher initial investment. Both panel types require minimal maintenance; occasional cleaning and inspections are generally sufficient. However, monocrystalline panels, due to their higher quality silicon, tend to have a slightly longer lifespan, potentially delaying or reducing the need for panel replacement. This longer lifespan contributes to the overall long-term cost savings. Replacement costs, while infrequent, should be considered in a comprehensive ROI analysis.
Return on Investment (ROI) Calculation Over 25 Years
The following table provides a simplified example of ROI calculations for both panel types over a 25-year period. These figures are estimates and will vary based on factors like energy production, electricity rates, government incentives, and system size.
Factor | Polycrystalline | Monocrystalline |
---|---|---|
Initial System Cost | $12,000 | $15,000 |
Average Annual Energy Savings | $1,000 | $1,200 |
Total Energy Savings (25 years) | $25,000 | $30,000 |
Net Savings (Total Savings – Initial Cost) | $13,000 | $15,000 |
Simple ROI (Net Savings / Initial Cost) | 108% | 100% |
Note: This table presents a simplified ROI calculation. A more detailed analysis would incorporate factors such as inflation, interest rates, potential maintenance costs, and degradation rates of the panels over time. Consult with a financial advisor for a personalized ROI assessment.
Appearance and Aesthetics

The visual differences between monocrystalline and polycrystalline solar panels significantly impact their aesthetic appeal and suitability for various applications. Understanding these differences is crucial for homeowners and businesses seeking to integrate solar energy seamlessly into their property’s design.
Monocrystalline panels are characterized by their uniform, dark-blue, almost black color. This is due to the single-crystal silicon structure used in their manufacturing. Their consistent color creates a sleek, modern appearance. In contrast, polycrystalline panels exhibit a mottled, bluish-grey appearance due to the multiple silicon crystals used in their production. These variations in color and texture give them a less uniform look.
Visual Differences and Their Impact on Residential and Commercial Applications
The distinct visual characteristics of monocrystalline and polycrystalline panels influence their suitability for different settings. The sleek, uniform appearance of monocrystalline panels often aligns better with modern architectural styles, making them a popular choice for residential homes aiming for a clean, sophisticated look. Their dark color can also absorb more heat, which might be a consideration in certain climates. Conversely, the less uniform look of polycrystalline panels might be less noticeable on larger commercial rooftops or in less aesthetically-focused settings. The cost difference often plays a role here, with polycrystalline panels being a more budget-friendly option, potentially justifying their less refined appearance in some large-scale projects.
Examples of Panel Type Influence on Solar Installation Design
Consider a modern, minimalist home with a pitched roof. The dark, uniform appearance of monocrystalline panels would complement the home’s clean lines and architectural style, integrating seamlessly into the overall design. Conversely, a large warehouse with a flat roof might utilize polycrystalline panels due to their lower cost. The less uniform appearance of the panels would be less noticeable on such a large surface area, and the overall visual impact is less critical than cost-effectiveness in this scenario. A historic building undergoing renovation, on the other hand, might require careful consideration of both panel type and installation method to minimize visual disruption to the building’s original aesthetic. The choice might lean towards a panel type and mounting system that best blends with the existing architectural style, regardless of cost considerations.
Environmental Impact
Choosing between monocrystalline and polycrystalline solar panels involves considering their environmental impact throughout their entire lifecycle. Both types contribute to reducing reliance on fossil fuels, but their manufacturing processes and material requirements differ, leading to variations in their overall environmental footprint. Understanding these differences is crucial for making an informed decision that aligns with sustainability goals.
The environmental impact of solar panel production encompasses several key factors, primarily energy consumption during manufacturing and waste generation. Monocrystalline silicon production requires a more energy-intensive process compared to polycrystalline silicon, resulting in a higher carbon footprint during the manufacturing phase. However, monocrystalline panels generally exhibit higher efficiency, potentially offsetting some of this initial energy burden over their operational lifespan. Polycrystalline panels, while less energy-intensive to produce, may require a larger surface area to achieve the same power output, leading to increased land usage and potentially higher transportation emissions. Waste generation is another important consideration; both panel types generate waste during manufacturing and at the end of their life cycle, although recycling initiatives are constantly evolving to minimize this impact.
Manufacturing Energy Consumption and Waste Generation
The manufacturing processes for monocrystalline and polycrystalline silicon differ significantly, impacting energy consumption and waste generation. Monocrystalline silicon involves a more complex and energy-intensive process, requiring higher temperatures and more refined purification techniques. This leads to greater energy consumption and potentially more greenhouse gas emissions during manufacturing. Polycrystalline silicon, on the other hand, uses a less energy-intensive process, resulting in lower energy consumption and fewer greenhouse gas emissions during production. However, the less refined nature of polycrystalline silicon can lead to higher material waste during the manufacturing process. Both processes generate silicon waste, but the volume and type of waste vary depending on the manufacturing techniques and efficiency. Ongoing research focuses on improving recycling methods for silicon waste to minimize the environmental impact.
Carbon Footprint Across the Lifecycle
The carbon footprint of a solar panel encompasses the emissions associated with its entire lifecycle, from raw material extraction and manufacturing to transportation, installation, operation, and eventual disposal. While both monocrystalline and polycrystalline panels contribute to reducing carbon emissions by generating clean energy, their lifecycle carbon footprints differ. Studies have shown that monocrystalline panels tend to have a slightly higher carbon footprint during the manufacturing phase due to the higher energy consumption involved. However, their higher efficiency translates to less land usage and potentially lower transportation emissions. Furthermore, their longer lifespan can lead to a lower overall carbon footprint over their lifetime compared to polycrystalline panels that might need replacement sooner. Accurate comparisons require considering the specific manufacturing processes, energy sources used, and the geographical location of production and operation. For example, a monocrystalline panel manufactured using renewable energy sources would have a significantly lower carbon footprint than one manufactured using fossil fuels.
Sustainability Advantages and Disadvantages
The following table summarizes the sustainability advantages and disadvantages of monocrystalline and polycrystalline solar panels:
Feature | Monocrystalline | Polycrystalline |
---|---|---|
Manufacturing Energy Consumption | Higher | Lower |
Waste Generation | Potentially Lower (depending on efficiency) | Potentially Higher |
Efficiency | Higher | Lower |
Land Use | Lower (for same power output) | Higher (for same power output) |
Lifespan | Generally Longer | Generally Shorter |
Cost | Generally Higher | Generally Lower |
Carbon Footprint (Overall) | Potentially Lower (due to higher efficiency and longer lifespan) | Potentially Higher (due to lower efficiency and shorter lifespan) |
It is important to note that the overall environmental impact of each panel type is influenced by numerous factors and these comparisons represent general trends. Specific environmental impacts vary depending on manufacturing processes, geographical location, and end-of-life management practices.
Durability and Longevity
Choosing between monocrystalline and polycrystalline solar panels often involves considering their long-term performance and resilience. Both types are designed for outdoor use and are expected to withstand various environmental conditions, but their inherent properties lead to some differences in durability and longevity.
The longevity of a solar panel is significantly influenced by its ability to withstand environmental stressors such as extreme temperatures, humidity, and UV radiation. Both monocrystalline and polycrystalline panels are engineered to resist these factors, but their performance under duress varies.
Resistance to Environmental Factors
Monocrystalline panels generally exhibit superior resistance to high temperatures due to their uniform silicon structure. This uniformity contributes to better heat dissipation, reducing the risk of performance degradation under intense sunlight. Polycrystalline panels, with their slightly less uniform structure, may experience slightly greater performance loss in extreme heat. Similarly, monocrystalline panels often show better resistance to cold temperatures, maintaining higher efficiency levels in freezing conditions compared to polycrystalline panels. Both types are designed to withstand humidity, but prolonged exposure to high humidity may impact the performance of both types over a very long period, though this effect is typically minimal.
Potential Weaknesses and Vulnerabilities
While both panel types are robust, potential weaknesses exist. Microscopic cracks, sometimes present in polycrystalline silicon due to its manufacturing process, can potentially reduce the panel’s efficiency over time and increase vulnerability to moisture ingress. Monocrystalline panels, while generally more resistant to cracking, can be susceptible to damage from physical impacts, potentially leading to breakage or internal cell damage. The higher efficiency of monocrystalline panels, while beneficial, can also mean that a single cell failure can have a more significant impact on the overall system output compared to a polycrystalline panel with a similar failure.
Warranty Periods and Expected Service Life
Manufacturers typically offer warranties of 25 years or more for both monocrystalline and polycrystalline solar panels, covering performance degradation and material defects. However, the actual service life can exceed the warranty period. Real-world data indicates that many solar panels, regardless of type, continue to function effectively for 30 years or longer, with performance degradation typically following a predictable curve. While some studies suggest a slightly longer lifespan for monocrystalline panels, this difference is often marginal, and both types can provide reliable power generation for decades under normal operating conditions. The ultimate lifespan is also highly dependent on factors like installation quality, environmental conditions, and maintenance practices. For example, panels installed in areas with frequent hailstorms might experience a shorter lifespan than those in milder climates, irrespective of their crystalline structure.
Suitable Applications
Choosing between monocrystalline and polycrystalline solar panels often depends on the specific needs of the installation. Factors such as budget, available space, energy requirements, and aesthetic preferences all play a significant role in determining the optimal panel type for a given project. This section will explore the ideal applications for each type, considering geographical location and climate as well.
Monocrystalline Solar Panel Applications
Monocrystalline panels, due to their higher efficiency and power output, are particularly well-suited for situations where space is limited or maximum energy production is crucial. Their superior performance makes them a favorable choice for residential rooftops in urban areas, where maximizing energy generation from a smaller footprint is essential. Furthermore, their sleek, uniform appearance is often preferred in aesthetically sensitive locations.
Polycrystalline Solar Panel Applications
Polycrystalline solar panels, while slightly less efficient than their monocrystalline counterparts, offer a compelling cost advantage. This makes them an excellent choice for large-scale projects such as solar farms or commercial installations where the overall cost of the system is a primary concern. Their robustness also makes them suitable for applications in harsher environments where minor variations in cell performance might not significantly impact the overall system output.
Geographical and Climatic Considerations
The suitability of each panel type can also vary based on geographical location and climate conditions. In regions with abundant sunshine and high temperatures, such as those found in the southwestern United States or parts of Australia, the higher efficiency of monocrystalline panels may lead to greater energy production over the panel’s lifetime, justifying the higher initial cost. Conversely, in regions with less intense sunlight or frequent cloud cover, the cost difference between monocrystalline and polycrystalline panels might be less significant, making polycrystalline a more economically viable option. For example, a large-scale solar farm in a less sunny area might benefit more from the lower cost of polycrystalline panels, offsetting the slightly lower energy yield per panel. The long-term energy production and return on investment would need to be carefully modeled for each specific location and climate.
Technological Advancements
The solar panel industry is a dynamic field, constantly evolving with advancements in both monocrystalline and polycrystalline silicon technology. These improvements drive increased efficiency, reduced manufacturing costs, and enhanced durability, impacting the market share of each panel type. Understanding these technological leaps is crucial for anyone considering a solar energy investment.
Recent advancements in monocrystalline silicon technology have focused on improving the crystal structure and reducing defects to maximize light absorption. This has led to higher efficiency cells, often exceeding 22%, compared to the typical range of 15-17% for polycrystalline cells. Meanwhile, polycrystalline technology has seen advancements in improving the grain size and uniformity of the silicon, which helps to reduce energy losses and improve overall efficiency. However, the inherent limitations of polycrystalline silicon’s structure mean it is unlikely to ever match the efficiency levels of monocrystalline cells.
Efficiency Enhancements
Several techniques contribute to efficiency gains. For monocrystalline panels, advancements in wafering techniques create thinner, more efficient cells while reducing material waste. Passivation layers, applied to the cell surface, minimize electron-hole recombination, boosting the overall power output. In polycrystalline panels, advancements in casting techniques create larger and more uniform grains, resulting in improved light absorption and reduced internal losses. Perovskite solar cells, a promising emerging technology, are being explored as a potential addition or replacement for silicon in both monocrystalline and polycrystalline structures, offering the potential for significantly higher efficiencies in the future. This technology is still in its early stages of development but has shown rapid progress in recent years.
Manufacturing Process Improvements
Significant progress has been made in reducing the manufacturing costs of both panel types. Automation and improved production processes have streamlined the manufacturing of both monocrystalline and polycrystalline cells, making solar energy more accessible. The development of more efficient and less energy-intensive manufacturing techniques also reduces the overall environmental footprint of solar panel production. For example, advancements in chemical vapor deposition techniques for monocrystalline silicon production have reduced energy consumption and waste. Similarly, improvements in the casting process for polycrystalline silicon have resulted in higher yields and reduced production costs.
Timeline of Key Milestones
The development of both monocrystalline and polycrystalline solar cell technologies has been a gradual process, marked by several key milestones:
Year | Monocrystalline Technology | Polycrystalline Technology |
---|---|---|
1950s | Early research and development of single-crystal silicon solar cells. | Initial exploration of polycrystalline silicon for solar cells. |
1960s-1970s | Development of improved crystal growth techniques (e.g., Czochralski method). Increased efficiency but high cost. | Cost-effective production methods begin to emerge, making polycrystalline cells more commercially viable. |
1980s-1990s | Further efficiency improvements through advancements in surface passivation and anti-reflective coatings. | Improvements in grain size and uniformity lead to gradual efficiency gains. |
2000s-Present | Continued focus on reducing manufacturing costs and improving efficiency through advanced wafering and cell processing techniques. Exploration of tandem cells and other advanced architectures. | Ongoing efforts to improve efficiency and reduce costs. Focus on increasing grain size and reducing defects. |
Maintenance and Cleaning
Both monocrystalline and polycrystalline solar panels require minimal maintenance to ensure optimal performance and longevity. Regular cleaning is the most crucial aspect, as accumulated dirt, debris, and bird droppings can significantly reduce energy production. While the cleaning process is largely similar for both types, understanding the nuances can help optimize your panel’s lifespan and efficiency.
Regular cleaning of your solar panels is essential for maximizing energy production and extending their lifespan. Dirt, leaves, bird droppings, and other debris can significantly reduce the amount of sunlight reaching the solar cells, leading to a decrease in energy output. The frequency of cleaning depends on your location’s climate and environmental conditions; areas with frequent rainfall may require less frequent cleaning than drier, dustier regions.
Cleaning Procedures for Monocrystalline and Polycrystalline Solar Panels
The cleaning process for both monocrystalline and polycrystalline solar panels is virtually identical. The key is to use gentle methods to avoid scratching the delicate surface of the panels. Harsh chemicals or abrasive materials should be strictly avoided.
Recommended Cleaning Procedures
Prior to cleaning, always ensure the panels are cool to the touch to prevent damage. Never clean panels during a storm or when the surface is wet.
- Prepare your cleaning solution: Use a mixture of warm water and a mild dish soap. Avoid using harsh chemicals, abrasive cleaners, or ammonia-based products. A simple solution of one tablespoon of dish soap per gallon of water is usually sufficient.
- Gather your supplies: You will need a soft-bristled brush (a long-handled brush is ideal for reaching panels on rooftops), a bucket, a garden hose with a spray nozzle (or a pressure washer set to a low pressure setting), and a soft cloth or sponge for rinsing.
- Inspect the panels: Before starting, visually inspect the panels for any significant damage or loose debris. Remove any large debris such as leaves or branches by hand.
- Rinse the panels: Gently rinse the panels with water to remove loose dirt and debris. Avoid using high-pressure water, which could damage the panels.
- Apply cleaning solution: Dip your brush or sponge into the cleaning solution and gently scrub the panels in a back-and-forth motion. Avoid excessive scrubbing, which could scratch the surface.
- Rinse thoroughly: Rinse the panels thoroughly with clean water to remove all traces of soap. Ensure all soap residue is removed to prevent spotting.
- Dry the panels: Allow the panels to air dry if possible. If necessary, use a soft cloth to gently wipe away any remaining water droplets. Avoid using abrasive cloths or towels.
Frequency of Cleaning
The ideal cleaning frequency depends on several factors including climate, location, and the presence of trees or other shading elements. As a general guideline, cleaning your solar panels every 3-6 months is usually sufficient for most homeowners. However, in areas with high levels of dust or pollution, more frequent cleaning may be necessary to maintain optimal performance. For instance, a desert environment might require quarterly cleaning, while a location near a forest might need cleaning only once or twice a year.
Installation Considerations
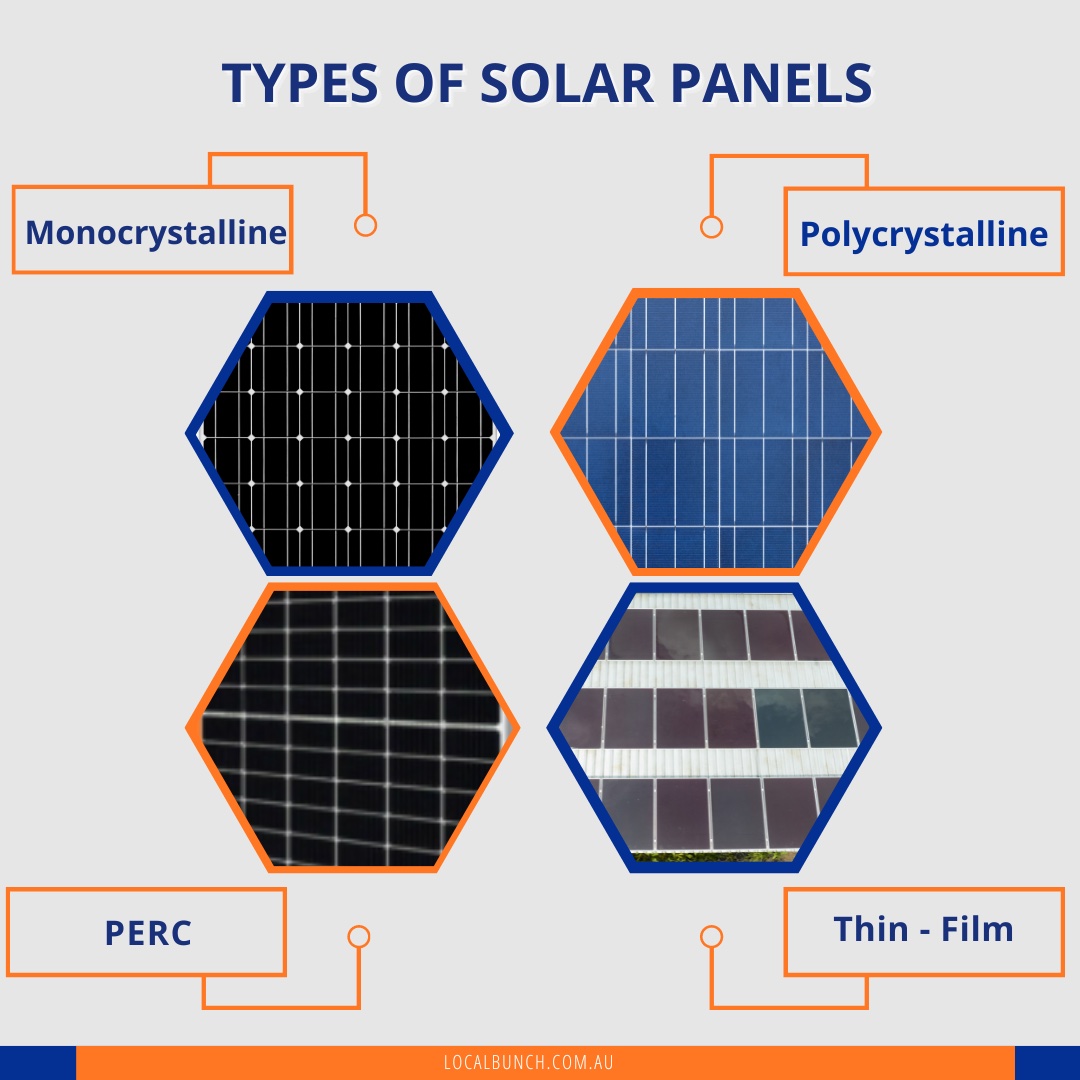
The installation of both monocrystalline and polycrystalline solar panel systems involves similar fundamental steps, but subtle differences exist due to the panels’ physical characteristics and potential weight variations. Understanding these differences is crucial for efficient and safe installation, impacting both the time required and the overall cost.
Installation procedures for both monocrystalline and polycrystalline solar panel systems generally involve site assessment, racking system installation, panel mounting, wiring, and connection to the inverter and electrical grid. However, the specific techniques and challenges can vary depending on factors like roof type, shading conditions, and the size of the system. The weight difference between the two panel types, although often marginal, can influence the structural requirements of the racking system.
Installation Procedures
Monocrystalline and polycrystalline solar panel installations follow a largely similar process. Both begin with a thorough site assessment to determine the optimal panel placement for maximum sunlight exposure and to ensure the roof or ground structure can support the system’s weight. This includes analyzing shading from trees, buildings, or other obstructions. Next, a racking system is installed to securely hold the panels at the correct angle. This system is tailored to the specific roof type and orientation. The panels are then mounted onto the racking system, ensuring proper spacing for ventilation and optimal performance. Wiring is meticulously done, connecting the panels in series and parallel to optimize voltage and current output. Finally, the system is connected to the inverter, which converts DC power from the panels to AC power for household use, and to the main electrical panel. Safety measures are crucial throughout the entire process, including using appropriate personal protective equipment (PPE) and adhering to electrical safety codes.
Installation Complexity and Labor Costs
While the fundamental steps are similar, some differences in installation complexity exist. Monocrystalline panels, often slightly heavier and more brittle than polycrystalline panels, might require more careful handling during installation to prevent damage. This can slightly increase labor costs, although the difference is often minimal for smaller residential systems. For large-scale commercial installations, however, the weight difference can become more significant, impacting the required labor and equipment. The overall labor cost also depends on factors like the complexity of the roof structure, the presence of obstructions, and the installer’s experience. Experienced installers are better equipped to handle potential challenges and complete the installation efficiently, regardless of the panel type.
Necessary Tools and Equipment
The tools and equipment required for both monocrystalline and polycrystalline solar panel installations are largely the same. Essential tools include measuring tapes, levels, drills, wrenches, screwdrivers, wire strippers, crimpers, multimeters, and safety equipment such as gloves, safety glasses, and fall protection gear. Specialized tools, such as a solar panel mounting system specific to the chosen racking system, are also necessary. For larger installations, equipment like lift systems or scaffolding might be required for safe and efficient work at height. The specific tools needed may vary slightly depending on the chosen racking system and the overall complexity of the installation. Proper calibration and maintenance of all tools are critical to ensure accuracy and safety during installation.
Choosing the Right Panel
Selecting between monocrystalline and polycrystalline solar panels requires careful consideration of several key factors. The optimal choice depends heavily on individual priorities, budget constraints, and the specific characteristics of the installation site. This section Artikels a framework to help consumers make an informed decision.
Factors Influencing Panel Selection
Consumers should prioritize their needs when choosing between monocrystalline and polycrystalline solar panels. This involves assessing the relative importance of factors such as energy production, initial cost, aesthetic preferences, and long-term performance. A balanced approach, considering all relevant aspects, is crucial for maximizing the return on investment.
Decision-Making Framework
A systematic approach to choosing between monocrystalline and polycrystalline solar panels involves evaluating several key criteria. The following framework helps consumers weigh the pros and cons of each option based on their specific circumstances.
A Visual Decision-Making Flowchart
Start → High Efficiency Required? → Yes: Monocrystalline → No: Consider Cost & Aesthetics → Budget Limited? → Yes: Polycrystalline → No: Monocrystalline (if aesthetics are important, consider black monocrystalline) → End
Alternatively, prioritize aesthetics and budget: High Aesthetic Importance and Budget Limited? → Yes: Polycrystalline → No: Consider Efficiency and Longevity → High Efficiency and Longevity Preferred? → Yes: Monocrystalline → No: Polycrystalline → End
These flowcharts provide a simplified visual representation of the decision-making process. However, detailed research and consultation with solar professionals are always recommended.
Specific Considerations
The choice between monocrystalline and polycrystalline solar panels should also account for factors like available roof space, the intensity of sunlight in the location, and the overall energy consumption needs of the household or business. For example, in areas with limited sunlight, the higher efficiency of monocrystalline panels might be a more significant advantage, justifying the higher initial cost. Conversely, in areas with abundant sunlight, the cost-effectiveness of polycrystalline panels might outweigh the slightly lower efficiency.
FAQ Insights
What is the lifespan of monocrystalline and polycrystalline solar panels?
Both types typically have a lifespan of 25-30 years, though their performance degrades gradually over time. Warranties often cover a significant portion of this period.
How much does installation cost?
Installation costs vary significantly depending on factors like system size, location, and installer. However, polycrystalline systems generally have a lower upfront cost than monocrystalline systems of equivalent power output.
Which type is better for hot climates?
Monocrystalline panels generally perform better in hot climates due to their higher efficiency and lower temperature coefficients. However, both types can function effectively with proper installation and ventilation.
Are there any government incentives for solar panel installation?
Many governments offer incentives like tax credits or rebates to encourage solar energy adoption. These incentives can vary by location and may apply to both monocrystalline and polycrystalline systems. Check your local regulations for details.